Direct Thermal vs. Thermal Transfer Printing
- TagMan
- Mar 26
- 3 min read
Printers are the backbone of efficient labeling in many industries, from retail and logistics to plant nurseries and horticulture operations. The right thermal printer can mean the difference between crisp, long-lasting prints and smudged, unreadable labels. But not all thermal printing methods are the same—choosing the right one is essential for durability, efficiency, and cost-effectiveness.
If you’ve ever struggled with faded or smudged prints, you know how frustrating it can be. The wrong printing method can lead to wasted supplies, inefficiencies, and even lost revenue. That’s why it’s important to understand the differences between direct thermal and thermal transfer printing before investing in a printer.
In this guide, we’ll break down how these two printing technologies work, their advantages and limitations, and which one is best suited for your business—whether you need long-lasting plant tags, barcode labels, or high-volume product labeling. Let’s dive in!
The Difference Between Direct Thermal vs. Thermal Transfer Printing
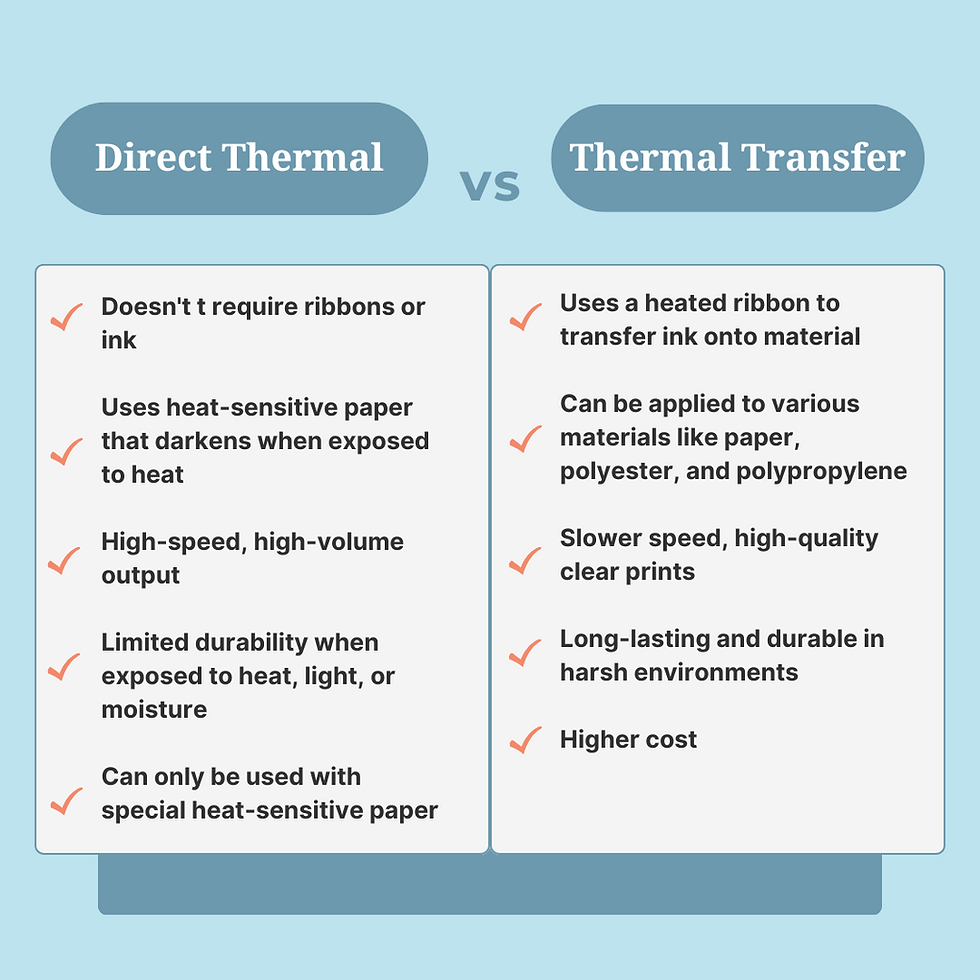
Both Direct Thermal and Thermal Transfer Printers use heat to create images, but they do so in very different ways. The key difference lies in how the image is transferred onto the label or tag.
Direct thermal printing uses heat-sensitive paper that darkens when exposed to heat.
Thermal transfer printing uses a ribbon to transfer ink onto the label material.
This fundamental difference impacts durability, cost, and application suitability.
What is Direct Thermal Printing?
Direct thermal printing is a straightforward method that doesn’t require ink, toner, or ribbons. Instead, it uses heat-sensitive paper that reacts to the heat applied by the print head. This method is commonly used for short-term labeling needs, such as shipping labels, receipts, or temporary barcodes.
Direct Thermal Printing Benefits and Limitations
Benefits:
Cost-effective: These printers don’t require ribbons or ink, lowering long-term expenses and reducing supply costs.
Simple to use: With fewer moving parts, they are easier to operate, require minimal training, and have lower maintenance needs.
Fast printing: They produce prints quickly, making them perfect for businesses needing high-speed, high-volume output.
Limitations:
Limited durability – Labels may lose their readability over time when exposed to heat, light, or moisture, making them unsuitable for long-term use.
Short-term use – These labels are ideal for temporary applications but are not durable enough for outdoor or long-term labeling, such as plant tags.
Material restrictions – They can only be used with special heat-sensitive paper, limiting their compatibility with other materials.
Key Takeaway: Direct thermal printing is great for temporary needs but falls short when durability is a priority.
What is Thermal Transfer Printing?
Thermal transfer printing, on the other hand, uses a heated ribbon to transfer ink onto the label material. This method is known for producing high-quality, durable prints that can withstand harsh environments. It’s widely used in industries like horticulture, manufacturing, and healthcare, where labels need to last.

Thermal Transfer Printing Benefits and Limitations
Benefits:
Durability: These labels are designed to withstand fading, moisture, and chemicals, ensuring they remain intact for long-term use.
Versatility: They can be applied to different materials like paper, polyester, and polypropylene, making them suitable for various applications.
High-quality prints: The labels produce sharp, clear, and professional-looking prints, enhancing readability and visual appeal.
Limitations:
Higher cost: Thermal transfer printing uses ribbons, which increase the overall printing expense over time.
More maintenance: Ribbons must be replaced frequently, adding to maintenance efforts and operational costs.
Slower speed: Printing takes slightly longer compared to direct thermal printing, reducing overall efficiency.
Key Takeaway: Thermal transfer printing is the go-to choice for businesses that need durable, high-quality labels.
Is Direct Thermal or Thermal Transfer Better for Plant Tags and Labels?

When it comes to plant tags and labels, durability is key. Labels must withstand outdoor conditions, including sunlight, water, and temperature changes. This is where thermal transfer printing shines.
Thermal transfer labels are resistant to fading and smudging, ensuring that your plant tags remain legible for years. They also offer greater flexibility in terms of materials, allowing you to choose the best option for your specific needs. Whether you’re labeling pot stakes, adhesive stickers, or wrap-around tags, thermal transfer printing delivers consistent, high-quality results.
When comparing direct thermal vs thermal transfer, direct thermal printing, while cost-effective, simply can’t match the durability and longevity of thermal transfer labels. For businesses in horticulture or nurseries, investing in thermal transfer printing is the preferred method.
Explore Thermal Transfer Printers by RealTimeTags

Choosing the right printing method can make all the difference in your labeling process. RealTimeTags provides cutting-edge thermal printing technology modified specifically for horticulture needs. Explore our range of thermal transfer printers to find the perfect solution for your business. Upgrade your thermal transfer labeling process and see the difference for yourself!
Comments